Double top construction
Double Top guitars, also called "composite top", or sandwich top" guitars, were pioneered by German Luthiers Gernot Wagner and Mathias Damman. Initially, Gernot used Nomex as the core material for his laminations, while Mathias experimented with wood as the core. But by the mid 90's both were using Nomex for the core material, rather than wood. Lighter weight can be had using Nomex, although many luthiers use balsa wood as a core material.Dominelli Double tops use a Nomex core. Nomex, a kevlar polymer, manufactured in a honeycomb pattern, originally developed for the aviation industry, gets sandwiched between two layers of spruce, cedar, or a combination of these two woods.
Nomex is a pretty amazing material to work with. I'm now able to create soundboards with a much higher stiffness to weight ratio. But unlike a lattice braced soundboard, double tops remain fairly thick, and so behave, acoustically speaking, much more like a traditional solid top guitar. My double tops have a very traditional sound - not a nasal or boomy sound like you might have heared on some other modern classicals.
Another advantage with nomex is, unlike wood, it is a man-made material. This helps achieve consistency in the sound from guitar to guitar. Achieving consistency of sound with solid wood tops is more difficult, no matter how carefully the woods are sourced.
Contrary to popular misconceptions (often the result of bad press by luthiers who do not make them) double tops are very durable. I've done extensive testing of the materials, and nomex double tops are extremely resistant to cracking compared to a traditional solid top guitar. Nomex is a tough, reliable material, with decades of use in the aeronautical industry.
Here's a quick overview of the process:
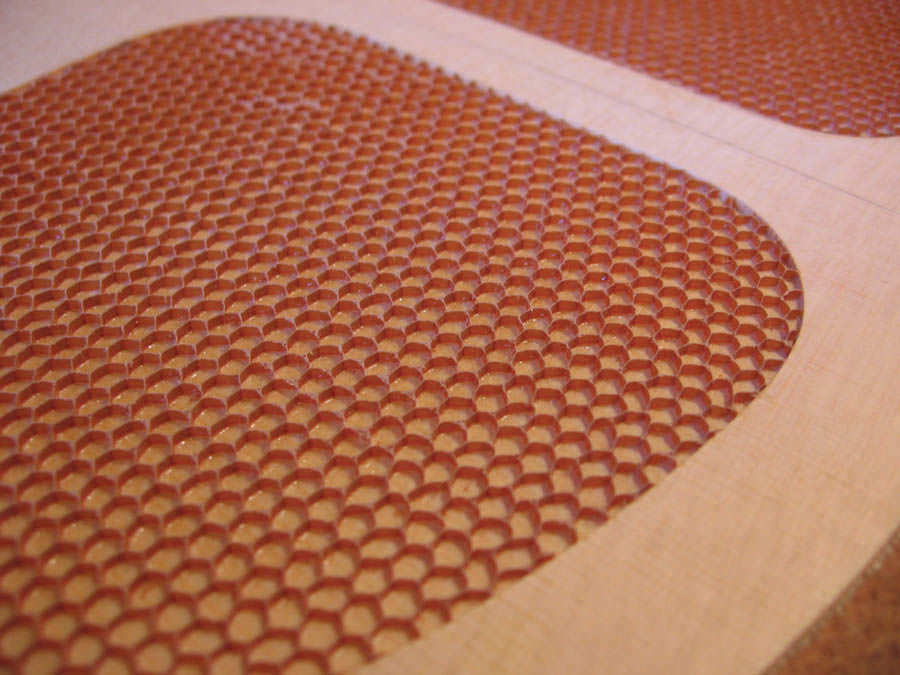
This image shows the nomex inlaid into the soundboard, in this case master grade lutz spruce, chosen for its lightweight and stiffness. Water based glues cannot be used, as they would cause the thin skins of wood to curl like a potato chip instantly. Epoxy or polyurethane are the glues of choice here.
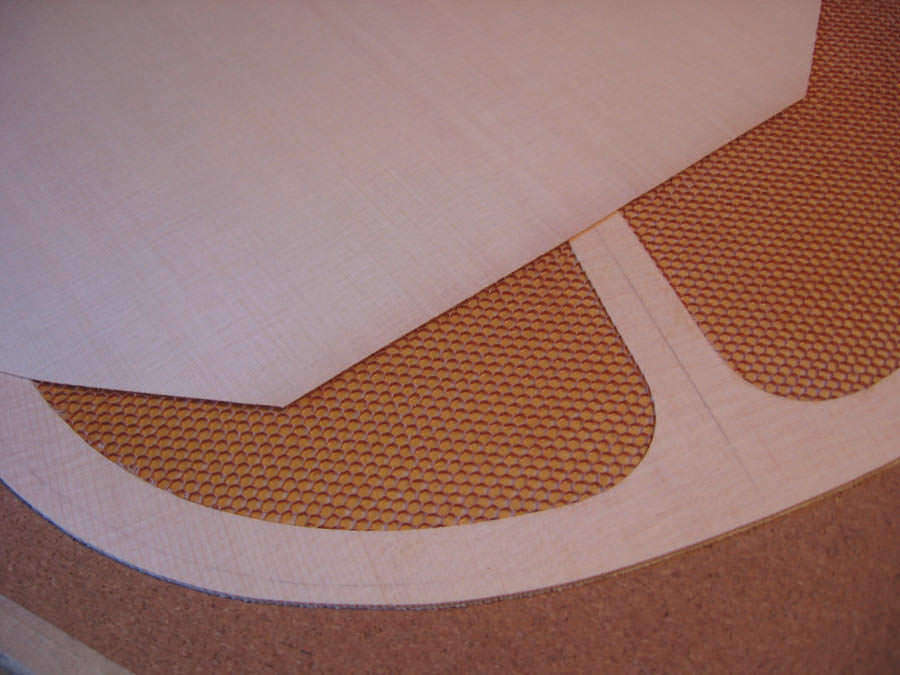
The second skin, shown here, will be glued onto the first lamination. Spruce or cedar can be used for either layer, depending on how I want the guitar to sound.
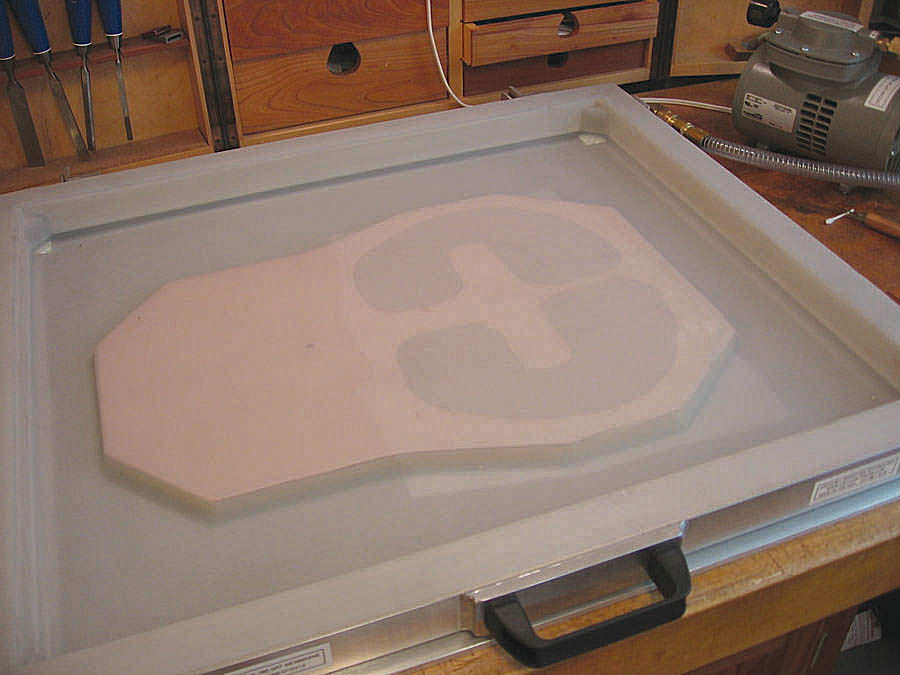
The laminations are glued up in a vacuum press, as shown here. This press was custom made for me, and features a neoprene membrane and a 3/8" thick aluminum platen. It does a great job; fast and user friendly.
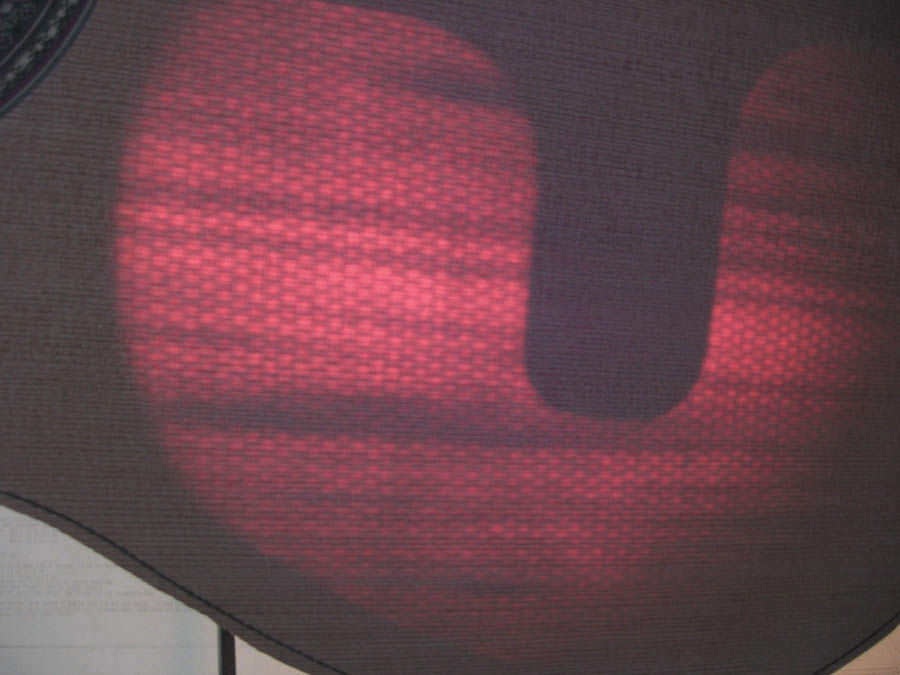
This image shows the finished lamination. I took this picture with a 100 watt light shining through the soundboard. The nomex will not be visible in the finished guitar, under normal daylight. The result is a stiffer, lighter soundboard, which is now ready for bracing, and later, assembly.